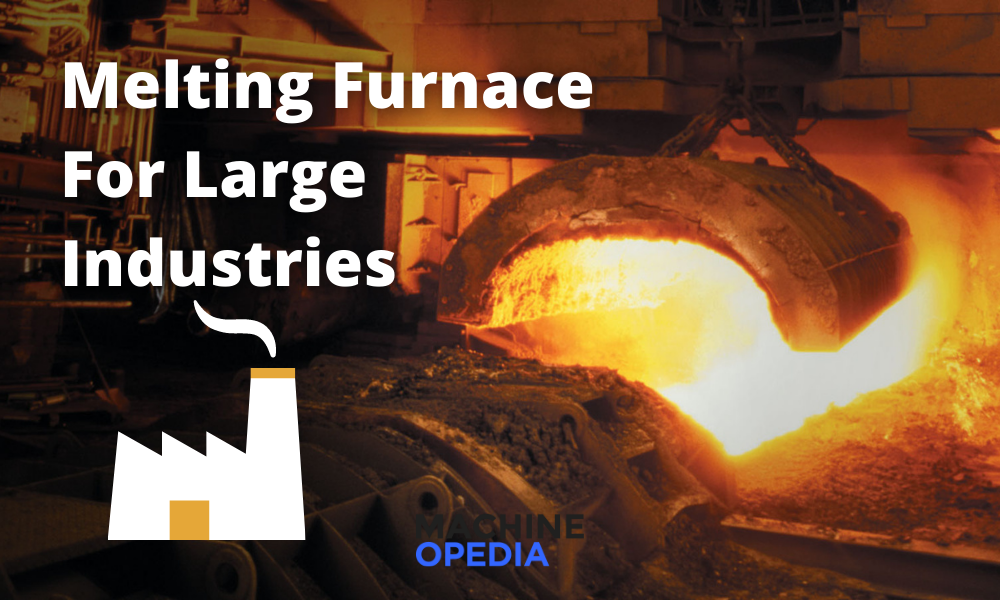
Melting furnaces are high-tech machines that heat objects to such an extent that they melt and turn into a liquid form chemical. This conversion from solid to liquid state becomes possible after those objects reach a certain specific threshold temperature. Also, different objects get melted according to their melting temperature. There is a wide variety of furnaces in the market with different sizes and capabilities, and each of them is intended to perform certain tasks. They can be employed for personal use and in private shops or garages. Mostly they are needed in the larger industries.
The most common materials used in the furnaces for melting are the metals, such as Aluminum, stainless steel, and other precious metals. Melting makes the formation, molding, and reconfiguration of the materials possible. The furnaces basically create the objects into something useful. Gold and silver are also melted in these furnaces, for instance, to make jewelry. According to history, however, the first melting furnace was developed in the Indus Valley Civilization of the Indian subcontinent almost in between 2500 to 1800 BC.
Before moving towards what types are used in the large industries, it is critical to note why those industries require such furnaces for the melting procedure. Here are discussed some of the optimal reasons that suggest why they are required in large industries.
The melting furnaces are known for their high efficiency. They melt the objects very quickly that leads to higher yield but with less burning loss. The reduced metal melting time proves the increased productivity and efficiency of the furnace.
As there is the least waste generated in the operation of melting, these melting furnaces have a lesser negative impact on the environment. Moreover, they are also less noisy.
The oxidation and cost losses are also reduced when large industries utilize such furnaces for the melting process.
Another reason that makes the bigger industries employ the melting furnaces is that the finishing is as perfect as desired.
The metallurgical function of the melting furnaces is also optimal.
Here is the list of the top industries that require the use of melting furnaces.
Coming towards the top melting furnaces that are required by the large industries for a wide range of applications. The different types of melting furnaces were invented with time as per the requirements of various applications. Here are described all the main melting furnaces required by the large industries.
Foundry industries are one of the biggest industries, and they require the use of Induction forging furnaces. The induction forging furnaces function by utilizing electric currents. The currents are what melts the steel at a certain temperature. The melting temperature of the steel is generally 1370 degrees Celsius, which is around 2500 degrees Fahrenheit. The point that makes them distinctive from other furnaces is that they employ coiled heating elements to be surrounded around a crucible that contains metal alloys and some of the additives. The metal is heated when charged. As this high-tech appliance can produce high-quality products, larger industries find the main reason to utilize it. Moreover, they are also super easy to operate with better metallurgical function.
Crucible furnaces are made to withstand the highest temperatures in large industries and which is why they are constructed of refractory materials, like ceramic, to make the mold. The crucible, which can be a cup-sized system or a large kiln furnace, is placed above the heat source to melt the different metal products inside. Additives and metal alloys are already kept inside it. The best thing about the crucible furnace is that it can melt metals of any size and is a user-friendly system. It is quite convenient to change the contents within. There are both resistance-heated and fuel-heated furnaces available for large industries as per their requirements. Not only this, but these furnaces are also categorized into some types, such as the fixed crucible furnaces, tiltable crucible furnaces, and movable crucible furnaces. All these crucible furnaces are known for their low maintenance, increased productivity, and simple operation.
Cupola steel melting furnaces are one of the oldest ones as they have been used in foundries for centuries to produce steel in massive amounts. Though, now there are better versions of them available for large industries with improved induction technology. They are basically chimney-like furnaces with a central dome lined with bricks and clays and constructed of sedimentary rocks. The interior walls of the cupola melting furnaces are protected from the enormous heat, oxidation, and abrasion. This cylindrically-shaped dome is further filled with steel alloys, coke, and limestone before the melting procedure starts. Furthermore, this addition leads to a chemical reaction in which all the filth in the kiln starts to glide on the metal furnace.
Electric arc furnaces are another most in-demand furnaces of the larger industries. Such furnaces generally use electrodes to run the electric current via the metal. For a further clear idea, the electric furnace basically employs the electrodes dipped in the metal to engender the heat required for its melting. For instance, the steel melting furnaces employ the carbon electrodes kept in the tank to charge the object straight until it melts. The electric arc furnaces are rampant among large factories that execute steel recycling operations. They can acquire 100 percent scrap metal recycling. Just like the other kilns, the electric arc foundries also differ in extent and design. These contemporary and highly efficient furnaces are known to heat up almost 400 tons of metal. Talking about the efficiency of the system, they let the smelters start and stop whenever required as the overall procedure is quite flexible and smooth.
Ashing furnaces are special and important furnaces that determine the contaminants in a sample. The samples they inspect are quite critical for every industry and every state, such as coal, petroleum products, and lubricating oils. As the name suggests, the sample is first burnt to produce the ashes. The reason is the contaminants in such samples can only be detected when the ashes are produced. This preconcentration technique is essential to check the trace elements before the chemical analysis.
Calcination furnaces are another critical furnace required in the larger industries, specifically for the preparation of raw materials. This heat-treatment technique is generally for raw processing or to retrieve the base material following other ways. In this method, various ceramic particles and minerals are exposed to the heat below the melting limit to cause phase transition, thermal decomposition, or the expulsion of volatile fractions.
Tempering is generally used to heat the steel at a certain specific temperature, which is then cooled inside the still air. Efficient tempering furnaces are necessitated in large industries for the iron-based alloys have been imperiled to hardening or quenching, which can also lead to excess robustness, pressure, and brittleness. However, the temperature at the object is heated to determines how much hardness is eradicated.
Annealing furnaces function in a bit different way as after heating up the object, they maintain its temperature before allowing it to cool at a suitable rate. This certain heat treatment mode is used to dissolve a specimen for better-quality cold working, machinability, as well as to intensify mechanical and electrical properties. Moreover, the annealing furnaces are also used at different temperatures and cooling rates as per the requirement of the application in different larger industries.
Sintering furnaces are another crucial kind of melting furnaces that are used to diminish the porosity of an object. Not only this, but these furnaces also improve the specific property of the object, including its thermal conductivity, strength, translucency, or electrical conductivity. The sintering procedure, however, is executed by first building and compacting a stable mass of the item using pressure or heat without softening the sample to the point of liquefaction.
Tensile testing furnaces are other furnaces needed in industries, particularly for measuring the final tensile strength, strain-hardening, product strength, and a range of other properties of any object. These furnaces are rampantly used as a testing way for quality assurance in massive factories. They look upon the sample to regulate tension until the total failure.
Rotary tube furnaces are the most versatile systems used for the fabrication of a variety of items, including alumina and cement clinker. But, besides the manufacturing, they are also required for oxidation in different factories. The specific trait of the Rotary tube furnaces is that they are round, and they constantly revolve during the heat treatment. These circular systems are generally used for continuous processing of the objects as they are able to deliver heat via several thermal control zones.
The aforementioned furnaces are the top most important furnaces for larger industries. However, there are other furnaces as well made by the melting furnace manufacturer that are needed by these massive industries. So, let’s have a glimpse at the other forges as well.
The world’s industrialization and modernization have become possible due to such advanced techniques. The melting of various metals, steel, gold, silver continues to play a leading role in the mechanization of the globe’s system. Therefore, the demand for such furnace systems upsurged critically over the last decade. This also manifests the importance of finding the right melting furnace because only the right system can help with myriad casting processes and manufacturing of products. So, if you are looking for such a reliable partner for the melting furnace business, then do not miss getting in touch with the well-known Electrical Machinery firm.
Shanghai Electrical Machinery Group Co., Ltd. is the foremost corporate of China that manufactures and supplies the highest quality of these furnaces. With years of experience, they have attained all the expertise in this field and gained abound customers from all the global platforms. Customers worldwide consider the Shanghai Electrical Machinery group the most reliable platform as they have always provided the best quality, best services, economical rates, and, most importantly, these efficient systems. The efficient melting furnaces they provide are quite productive in their performance and melt different materials for the manufacturing of various products. This firm is known to deal with and take projects from other large industries. Everyone can completely trust this corporate for the best services ever.
The world is running and developing due to the large industries of the contemporary world. It is mandatory that these industries are equipped with the perfect systems. Finding the ideal melting furnace has also become a crucial task for larger industries. This article definitely has helped you in finding the right one. There are a number of furnaces available with different variations in sizes, constructions, designs, etc. Molding, reformation, and recycling have become much easier because of the extra productivity of these systems. All one has to arrange is to find a trusted brand and manufacturer because having an efficient system would serve you for ages and profit your businesses at the max.