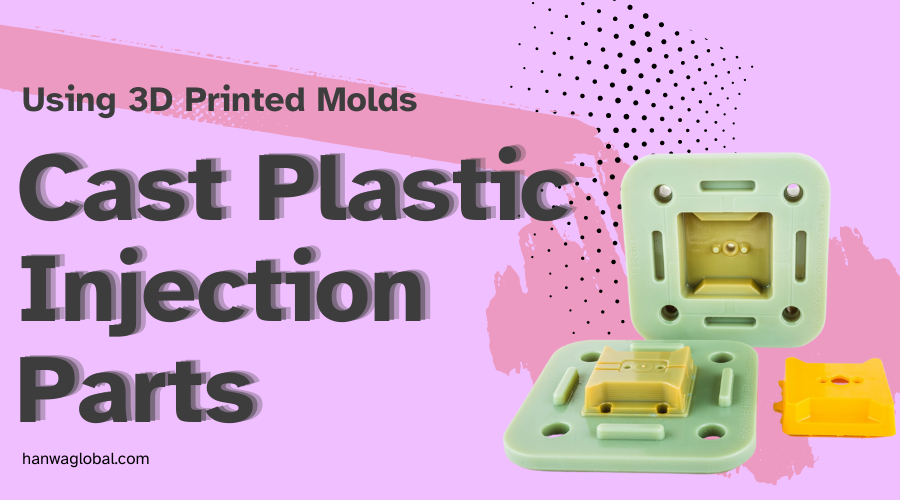
The synergy between 3D printing and plastic injection molding in manufacturing and rapid prototyping has opened up a world of possibilities. This innovative approach, often called 3D Print Mold for Casting, has revolutionized how custom plastic parts are created. By seamlessly combining the precision of 3D printing with the efficiency of plastic injection, manufacturers can produce intricate and high-quality components like never before.
Using 3D Printing for Casting is a game-changer in the manufacturing landscape. Traditional mold-making processes are often time-consuming and expensive. However, 3D printing has injected new flexibility and cost-efficiency into this arena. Manufacturers can design and produce intricate mold structures directly from a digital blueprint.
The process begins by designing a 3D model of the desired plastic part using computer-aided design (CAD) software. Once the design is ready, it's time to dive into the world of 3D printing. Manufacturers can use advanced 3D printers to create molds with astounding precision and complexity.
These custom plastic molds serve as the foundation for the plastic injection process. The mold is strategically designed to accommodate the molten plastic material, allowing it to cool and solidify into the intended shape. This process demands careful consideration of mold material, wall thickness, and venting systems to ensure optimal results.
The marriage of 3D printing and plastic injection molding ensures that each detail of the final part is replicated faithfully. This level of precision is particularly beneficial for industries where exact specifications are crucial.
The synergy between these technologies expedites the prototyping phase. Iterations and design modifications can be implemented swiftly, reducing lead times and costs associated with traditional tooling adjustments.
3D printed molds enable the creation of complex shapes and intricate geometries that would be challenging or impossible to achieve with traditional molds.
Traditional mold-making can be costly, especially for small production runs. 3D printing significantly lowers the upfront costs and minimizes material wastage.
The ability to quickly transition from design to mold to final product accelerates the time it takes to bring a product to market, giving businesses a competitive edge.
The applications of this innovative mold casting method span across various industries. From automotive to electronics, consumer goods to medical devices, manufacturers are reaping the rewards of the 3D Print for Molds approach. It's particularly beneficial for projects requiring intricate parts, customized components, and even small-batch production runs.
As technology evolves, the marriage between 3D printing and plastic injection molding will grow stronger. The era of plastic injection parts production is being defined by this fusion, with its cost-efficiency, speed, and precision paving the way for a more agile and creative manufacturing landscape.
In conclusion, casting plastic injection parts using 3D-printed molds is a revolutionary leap forward in the manufacturing world. With the ability to create intricate designs, reduce costs, and accelerate the production cycle, this approach reshapes industries. It allows manufacturers to bring their ideas to life with unprecedented precision and efficiency. As we navigate the ever-evolving landscape of technology, the synergy between 3D printing and plastic injection molding stands as a beacon of innovation and progress.
3D printing has its strengths, particularly with rapid prototyping and creating complex designs. However, it might only partially replace injection molding, especially for large-scale production. Hanwa Global approach combines the precision of 3D printing with the efficiency of injection molding, offering a compelling solution that maximizes the benefits of both technologies.
Creating plastic injection molds involves several key steps:
~ Design: Create a detailed 3D model of the desired plastic part using CAD software.
~ Material Selection: Choose a suitable material for the mold, considering factors like temperature and pressure compatibility.
~ 3D Printing: Utilize 3D printing technology to manufacture the mold based on the 3D model. Ensure a high-quality surface finish.
~ Mold Preparation: Inspect and refine the 3D printed mold, addressing imperfections or roughness.
~ Plastic Injection: Inject molten plastic material into the mold at high pressure, allowing it to fill every cavity.
~ Mold Removal and Finishing: Open the mold to release the molded plastic part, remove excess material, and perform the necessary finishing steps.
Combining 3D printing and plastic injection molding in creating plastic injection molds brings efficiency and precision to the process.
Using injection molds involves a precise process to create plastic parts. The molten material is injected into the mold at high pressure. Once cooled, the mold is opened, revealing the formed part. This method is essential in mass-producing items with consistency and accuracy.