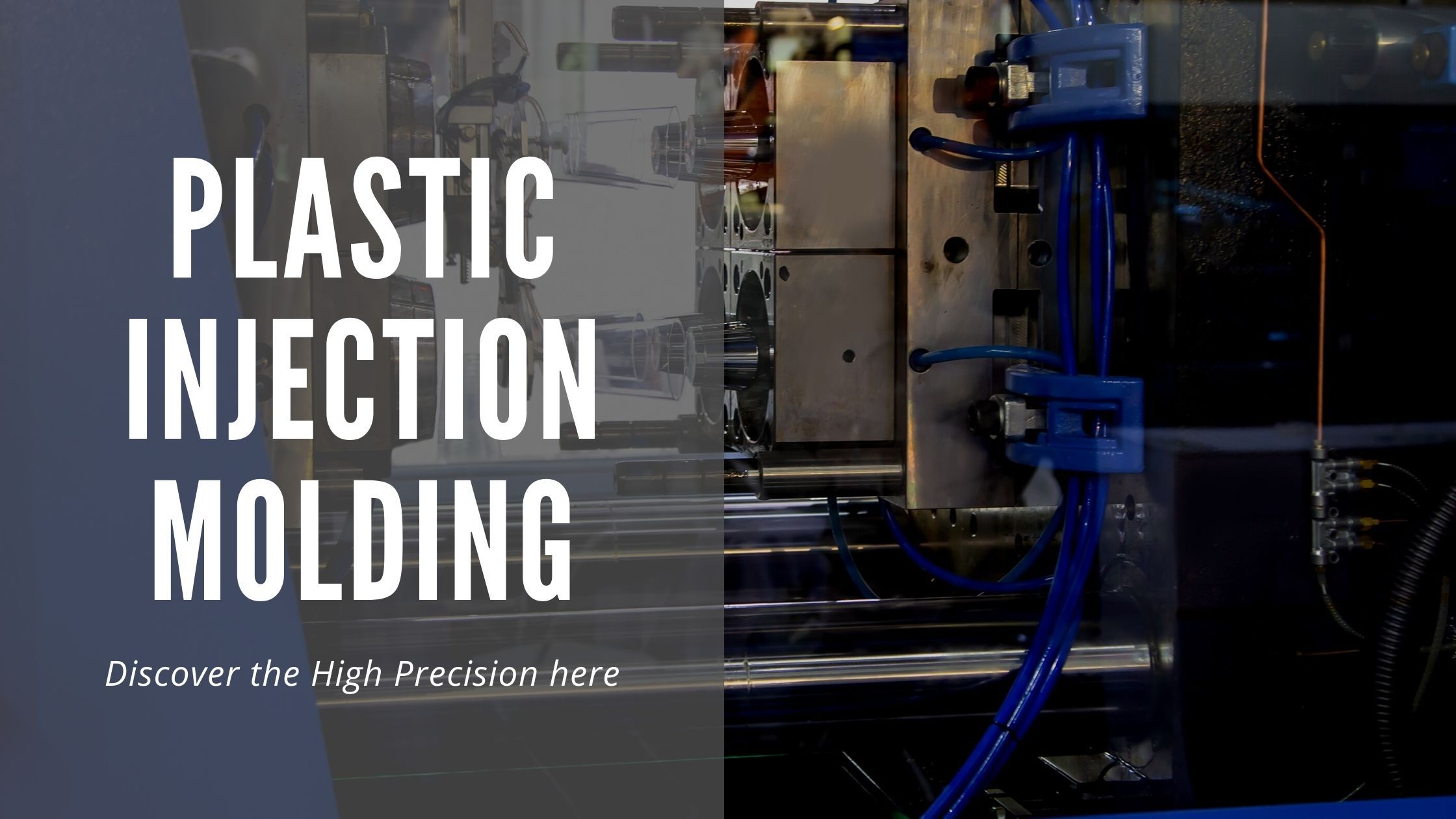
Molding is one of the most common manufacturing processes used in products today. It's a simple process that uses pressure and heat to create objects out of plastic. But there are different molding processes you can use to create different types of products. And each has its own set of advantages and disadvantages. In this guide, we'll walk you through the high-precision plastic injection molding process options available today so you can choose the right one for your company. Picking the Right Molding Process for a Particular Product As we noted above. There is a wide range of molding processes. You can use it to create plastic products with different looks and feel, performance levels, and costs.
Precision plastics are made with extremely tight tolerances, meaning that the final product will be very close to the original design. This is important for products that need to look and feel perfect, like eyeglasses or medical equipment. Standard plastic, on the other hand, is less precise and may have slight deviations from the original design.
One of the main benefits of using a precision plastics injection molding process is that it allows you to create very accurate objects. This means that your products are much more reliable and durable than those made with a standard plastic injection molding process. Another benefit of using a precision plastics injection molding process is that. It can be faster than other molding processes. This is thanks to the tight tolerances that are required for precision products. Plus, because precision plastic molds are much more difficult to damage, these processes can produce products with a longer lifespan than other types of plastic molds. Another benefit of precision plastics injection molding is that it results in a robust and stable product. Precision products do not crack or stretch as easily as standard products. This means that they can use for more extended and withstand high temperatures better than other types of plastic molds.
There are three main types of precision plastics injection molding processes blow Molding, Progressive Extrusion, and Injection Molding. Blow Molding is the simplest type of precision plastic injection molding process. This involves blowing a highly pressurized gas into the cavity of a molten plastic pellet to create the desired product. Blow Molding is often used for small articles that do not require complex shapes or multiple holes. Progressive Extrusion is slower than other types of precision plastic injection molding processes. This is because the molten plastic must first cool down to a temperature just below its melting point before it can then inject into the mold cavity. Progressive Extrusion also requires frequent cleaning mechanisms as each time products need to be removed from the molds could lead to voids in some parts of produced items. Injection Molding involves the injection of molten plastic into a die to create desired shapes. The low-pressure effects during injection allow for easy repeats operation. And thus, less frequent cleaning procedures are necessary.
The basic process flow for high precision plastics injection molding is as the customer provides a prototype or pre-production model to be made into a finished product. This is then used by the precision plastic injection molder to create a precise replica of the original model. Using one of three types of manufacturing processes blow Molding, Progressive Extrusion, and Injection Molding. Injection Molding is the most common type of precision plastic injection molding process. In this process, molten plastic is injected into a die to create the desired shape. Low pressure involved during injection allows for easy repeats operation, and thus less frequent cleaning procedures are necessary. Blow Molding is the simplest type of precision plastic injection molding process. It involves blowing a highly pressurized gas into the cavity of a molten plastic pellet to create the desired shapes. It is easy for us, and it involves less frequent cleaning procedures than the other two methods of precision plastic injection molding processes. Progressive Extrusion is similar to blow Molding in that both involve using highly pressurized gas pressure. Still, instead of blowing gas into something which was previously made from molten material, air or hot air is injected into what manufacturers inside an electric heating gun call an extruder. The extrudate is removed from the outside of the die. Allowed to cool and then placed into a mold cavity. In the Progressive Extrusion manufacturing process, machinery is used, which includes an injection system, stretching sequences in order to take on different shapes and geometries based on the necessity, and the various solvents volumes necessary for creating certain parts, as well glass beads or sand cores could include at specific points during this.